What is a 2 Plate Mould?
2 plate mould, also known as a two plate mold, is a type of injection molding mold used in the manufacturing process of plastic parts. It’s characterized by its relatively simple design, consisting of two main plates:
· Cavity Plate: This plate contains the cavity or impression of the final part to be molded. It defines the outer shape and surface finish of the plastic part.
· Core Plate: The core plate complements the cavity plate and creates the inner shape of the part. It often includes ejector pins or mechanisms to help remove the molded part once it has solidified.
How Does Two Plate Mould Work?
· The mold closes, with the cavity and core plates coming together to form a closed mold cavity.
· Plastic material, usually in the form of pellets, which injected into the cavity under high pressure through a nozzle and runner system.
· The plastic material fills the cavity and takes the shape of the part.
What is a 3 Plate Mold?
3 plate mold, also known as a three plate mold, is a type of injection molding mold used in the manufacturing process of plastic parts. Unlike the simpler 2 plate mold, the 3 plate mold has an additional plate, known as the runner plate or gating plate, which adds versatility to the molding process.
· Cavity Plate: This plate contains the cavity of the final part to be molded. It defines the outer shape and surface finish of the plastic part.
· Core Plate: Similar to the cavity plate, the core plate complements the mold and defines the inner shape of the part. It may include ejector pins or mechanisms for part removal.
· Runner Plate (Gating Plate): The runner plate, also known as the gating plate, is the distinguishing feature of a 3-plate mold. This plate creates a separate channel or runner system for the plastic material to flow into the cavity. It allows for multiple gating points, which can be strategically positioned for optimal material distribution and reduced cosmetic defects.
How Does Three Plate Mold Work?
· The mold closes, with the cavity, core, and runner plates coming together to form a closed mold cavity.
· Plastic material, typically in the form of pellets, is injected into the runner system under high pressure.
· The runner plate provides flexibility in gating options, allowing for the material to flow into the cavity through multiple points.
· After the material has cooled and solidified, the mold opens, and the finished part is ejected.
Differences Between Two-Plate and Three-Plate Injection Molds
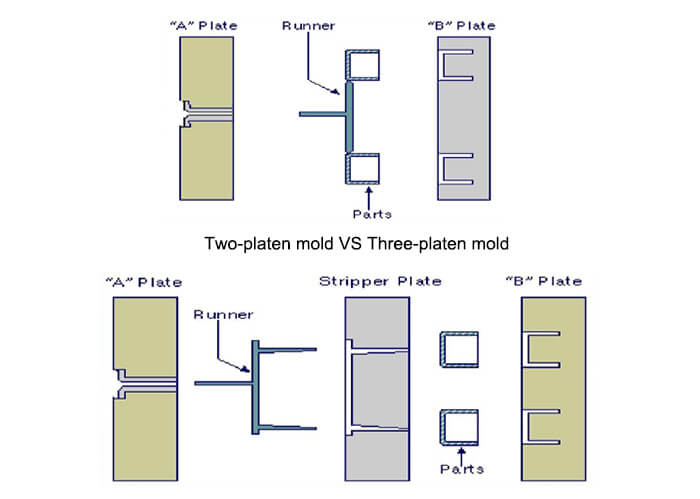
1. Basic Structural Differences
Feature | Two-Plate Mold | Three-Plate Mold |
Number of Parting Lines | 1 (between A plate moving and B plate fixed plates) | 2 (with an additional Stripper plate) |
Plate Composition | A Plate Fixed plate, B Plate moving plate | A Plate Fixed plate, Stripper plate, B Plate moving plate |
2. Runner and Product Separation Method
Two-Plate Mold:
· The runner (gate) and product are ejected on the same parting surface, typically using direct gates or edge gates. Submarine gates are often used for automatic demolding.
· Runners require subsequent trimming by manual, which may affect automation efficiency.
Three-Plate Mold:
· Runners and products are automatically separated through two parting actions: the first mold opening breaks the runner, and the second ejects the product.
· Suitable for pin-point gates, leaving minimal gate marks, ideal for appearance-sensitive products.
3. Mold Opening Sequence
Two-Plate Mold:
1. The moving plate and fixed plates separate directly, ejecting the product and runner together.
Three-Plate Mold:
1. First opening: The fixed plate separates from the stripper plate, breaking the gate, and the runner is ejected by the stripper plate.
2. Second opening: The runner plate separates from the moving plate, ejecting the product.
4. Advantages and Disadvantages Comparison
Type | Advantages | Disadvantages |
Two-Plate Mold | Simple structure, low cost, easy maintenance | Manual runner trimming required, visible gate marks, higher labor costs |
Three-Plate Mold | Automatic runner separation, high gate quality, suitable for precision parts | Complex structure, high cost, prone to failures, higher maintenance costs |
5. Typical Application Scenarios
Two-Platen Mold:
· Large parts with less strict gate location requirements (e.g., boxes, barrels).
· Low-precision or low-cost production needs.
Three-Platen Mold:
· Multi-cavity molds (e.g., bottle caps, electronic components).
· Products with high quality appearance requirements or hidden gates (e.g., transparent parts, consumer electronics).
6. Other Differences
· Mold Lifespan: Two-platen molds have simpler structures and generally longer lifespans; three-platen molds are prone to wear due to complex movements.
· Injection Machine Requirements: Three-platen molds require greater mold opening strokes.
Summary Selection Criteria
· Choose Two-Platen Mold: When prioritizing cost or producing large parts.
· Choose Three-Platen Mold: When pursuing automation, appearance quality, or high-efficiency multi-cavity production.